Tech notes
Wavelength Beam-Combined Laser Diode Arrays
Wavelength beam combining of diode lasers produces the intensity and brightness necessary for metal cutting and welding that previously required more powerful and more expensive laser systems.
The wavelength beam-combining fiber-coupled diode laser is the first direct-diode laser that is bright enough to cut and weld metal. Although diode lasers are the highest efficiency lasers, until recently their brightness has been relatively low compared to that of other kW-class lasers used in industrial applications. Lincoln Laboratory's fundamental breakthrough in wavelength beam-combining (WBC) has enabled the development of a system, shown in Figure 1, that has the laser brightness necessary for industrial use.
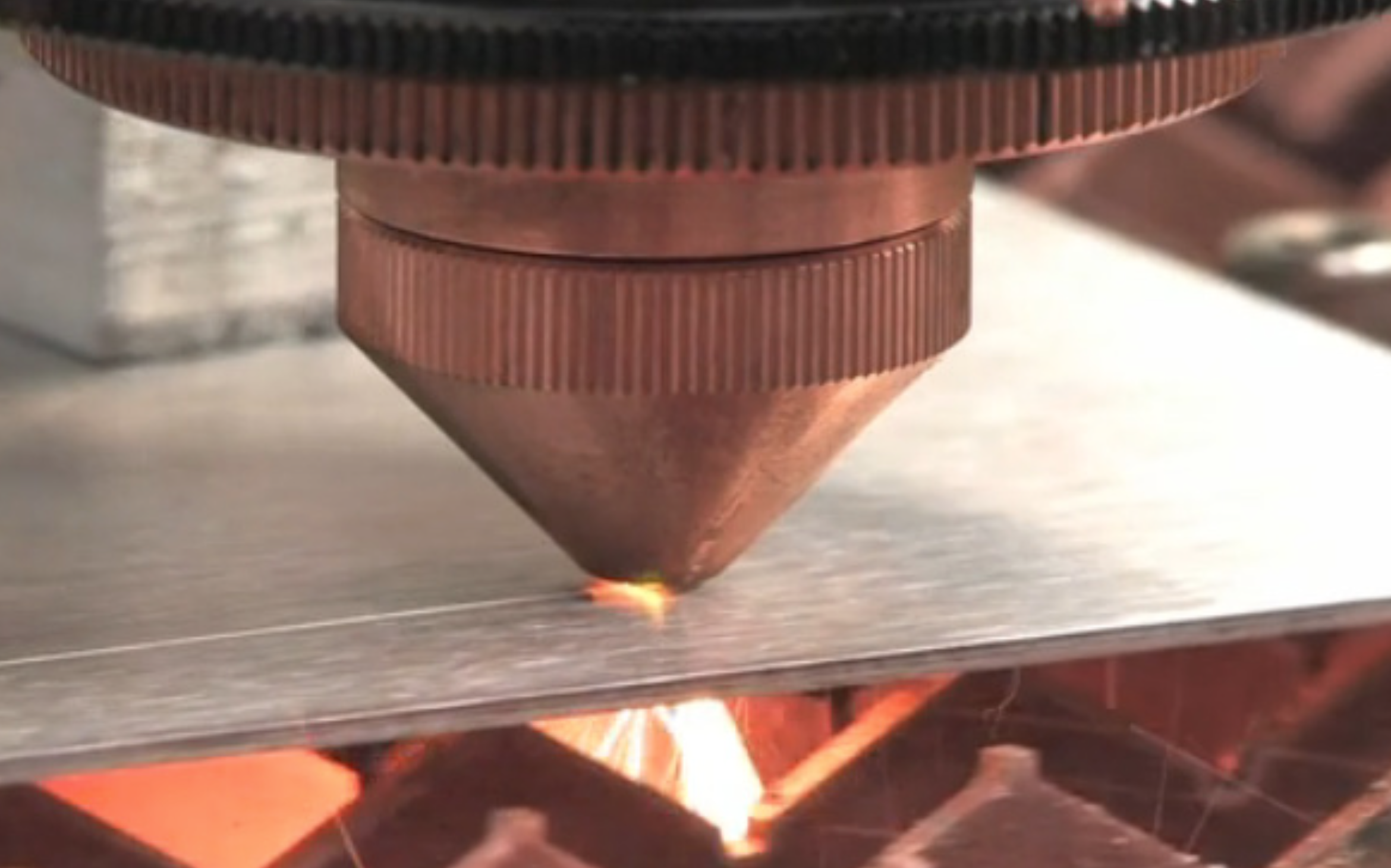
Intensity versus Brightness
Laser cutting and welding require that the intensity of the focused laser beam be sufficiently high so as to raise the temperature and locally melt the metal. A collimated laser beam is characterized by its power P, its beam diameter D (matching the size of the optical aperture), and its angular divergence, Ø, in the far field. It is a well-known fact that as a laser beam is transformed by an optical system, the product DØ is conserved; in going through the focusing optics, the beam is focused down to a spot d = D Ø/ where x is the focusing angle. The local intensity, I = P/d2, can then be expressed as I = P (x/(DØ))2 = Bx where B = P/(DØ)2 is defined as the laser beam brightness. An optical system with a given focusing angle x will then allow for local intensity proportional to the laser brightness. Brightness (not just power) determines the achievable intensity.
The Wavelength Beam-Combining Solution
WBC spatially merges multiple wavelength sources into a single high-intensity beam with an order-of-magnitude improvement in brightness compared to a single source. The fundamental building block of fiber-coupled diode lasers is the diode-laser bar. A diode-laser bar typically consists of an array (e.g., 19 elements over a typical 1 cm length) of electrically driven, edge-emitting, semiconductor lasers.
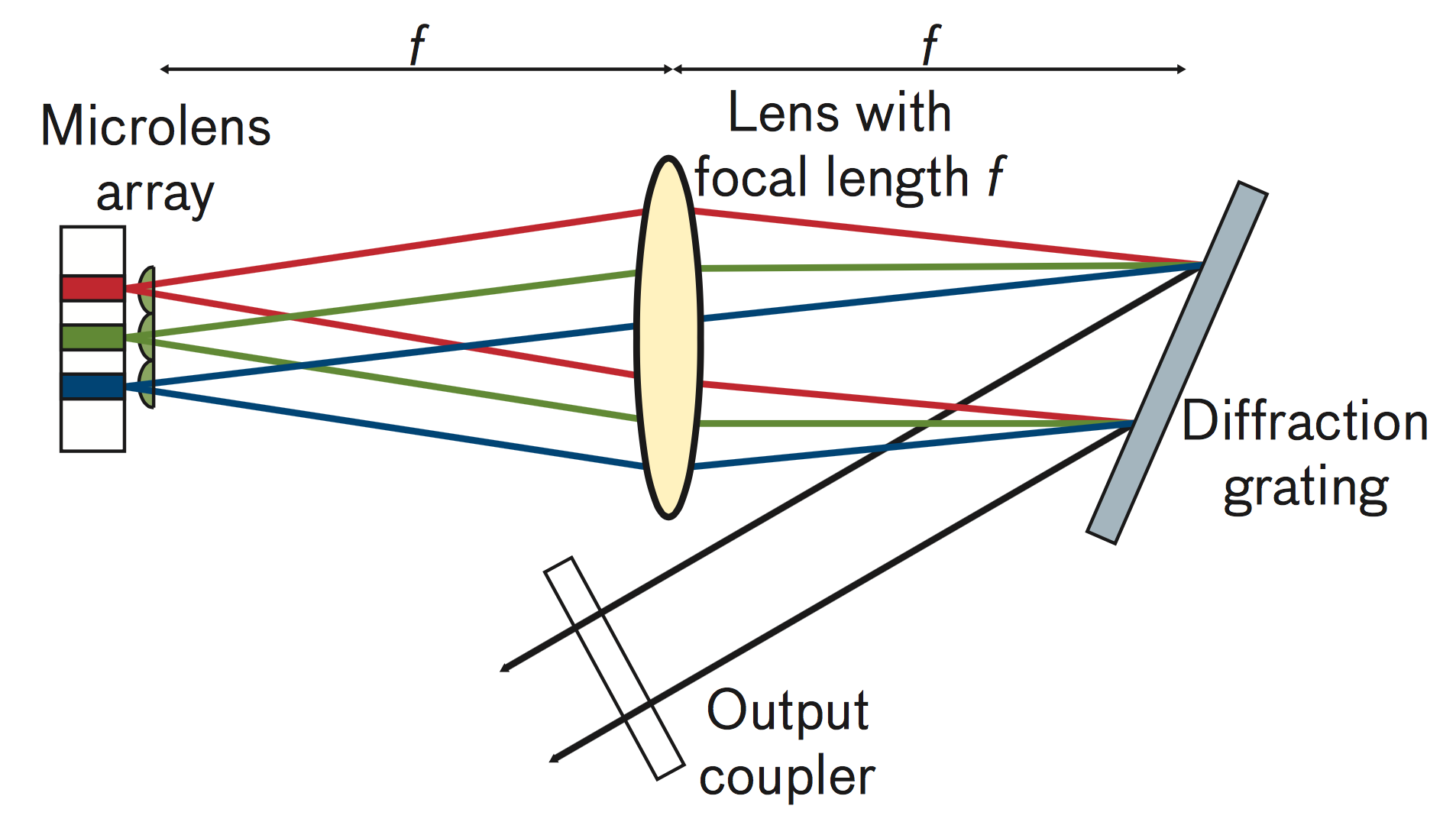
Conceptually, WBC can be thought of as the spatial superposition of many independent diode-laser external cavities. For simplicity, only three indepen- dent external cavities are shown in Figure 2. Each source is illustrated with a different color (red, green, and blue), which indicates a distinct wavelength characteristic to that external-cavity-stabilized diode laser element. Each cavity consists of an antireflection-coated and lensed laser gain element, a transform lens, a diffraction grating, and an output coupler. Figure 3 shows a tabletop version of the optical system.
The diffraction grating has an angle-to-wavelength conversion property that allows feedback to each diode-laser element in the array via the transform lens at a different wavelength. External cavity feedback is provided by the output coupler mirror. WBC allows for brightness scaling of a diode-laser array because all of the diode-laser elements are spatially overlapped at the output coupler, maintaining the output beam quality of a single element while scaling the output power by the number of elements in the array.
As the diode-laser array size increases, both the power and brightness of the output beam increase. Ultimately, the number of elements that can be combined is limited by the overall bandwidth of the semiconductor gain media and the bandwidth allocation per element (grating dispersion and resolution). For a typical semiconductor gain bandwidth of ~40 nm, an array with hundreds of elements could be wavelength beam combined.
Commercialization
The technology described above has been utilized by TeraDiode to develop the first direct-diode lasers that are bright enough to cut and weld metal. The 1 kW TeraDiode laser system cutting head is shown cutting through 0.26 inch steel plate in Figure 1. The entire system is mounted in a standard 19-inch rack. The laser is housed in a stainless steel enclosure. The system also includes the chiller and plumbing manifold, control computer, power supplies, power conditioning/distribution unit, and emergency stop switch. The output of the diode laser is coupled to a 200 µm core processing fiber, which has end connectors that are compatible with LLK-B industrial fiber connectors. The output end of the LLK-B fiber is coupled to a processing head, which can be configured for cutting or welding processes.
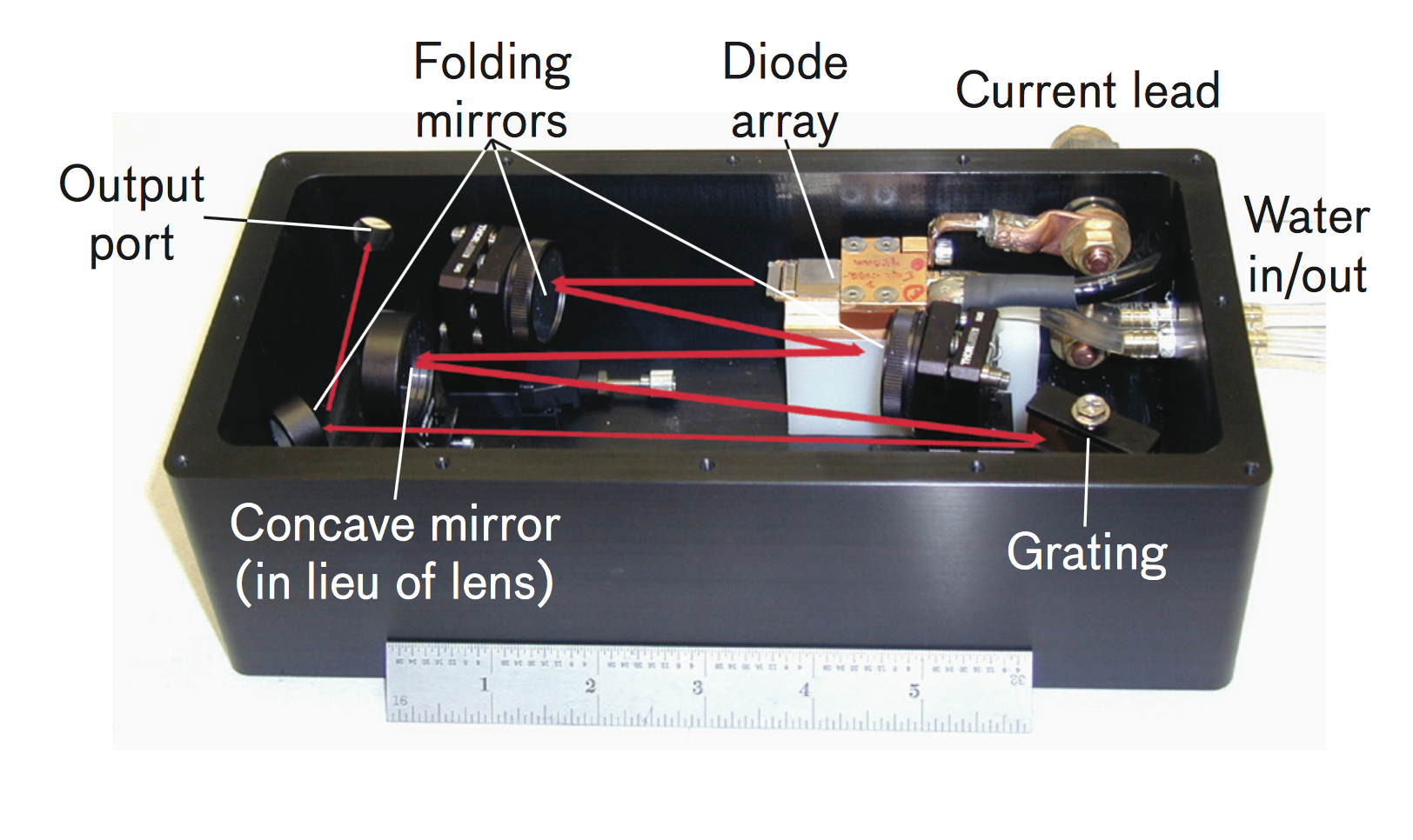
Industrial Applications
Multi-kilowatt-class lasers are used in cutting, welding, and other industrial applications where the high-intensity laser beam is used to locally raise the temperature of the material. These kW-class lasers include CO2, fiber, bulk solid-state lasers, and disk lasers.
In the past, individual diode lasers, while having a number of attractive features (they are compact, low-cost, reliable, and wavelength-versatile), were limited in power and brightness. Individual diode lasers are limited in power to the ~1 W class, and conventional diode laser arrays, used for power scaling, do not provide beams with the required brightness.
Compared to other direct-diode technologies in the kW-class, the WBC approach provides the very significant advantage of an order of magnitude increase in brightness over other direct-diode products. This high brightness enables the WBC technology to cut and weld metals.
Currently, CO2, fiber, and solid-state lasers are used for industrial applica- tions because they can generate high-brightness beams (high power with near diffraction-limited beams). When compared to these lasers, the WBC direct-diode technology offers a number of improvements:
- Higher efficiency when compared to diode-pumped lasers (fiber, solid state)
- Graceful degradation when some individual diodes age—no singlepoint of failure
- Ability to withstand unplanned (but typical) optical feedback—will not fail if optical feedback occurs from the metal sample being cut
- Relative lower cost
- Compact size
- Wavelength-versatility—may be important depending on the specific welding/cutting details (both the materials and the gas environment surrounding the beam)
The WBC technology combines high brightness, efficiency, and reliability with the power to perform the functions of current industrial lasers. Direct-diode lasers using WBC technology may also, in time, replace fiber, disk, and other lasers for the most demanding material-processing applications.
Posted 2012
top of page