Power to Go
Lincoln Lab–MIT collaboration challenges batteries with solar cells and a miniature burner.
An army on the go needs a lot of electricity—to operate radios, run computers, power autonomous vehicles. Batteries, useful as they are, are not the ideal power source; they can pack just so much energy into a given amount of material. Besides, they can slow soldiers up, or weigh them down. “Either batteries have to be recharged, or you just have to carry a whole lot of batteries,” says Christine Wang, a materials scientist in Lincoln Laboratory’s Electrooptical Materials and Devices group.
Wang has teamed up with Klavs Jensen, the Lammot du Pont Professor of Chemical Engineering at MIT, to provide a new lightweight source of portable power. Their method: combine a tiny butane burner built at Jensen’s lab with an infrared-sensitive solar cell that Wang and her colleagues have developed. “You’re basically taking thermal energy and converting it to electrical energy,” Wang says. Wang is using her experience developing photovoltaic cells over 10 years as part of a Department of Energy project. DOE wanted to develop technology to convert thermal energy directly into electricity. To do so required development of thermophotovoltaic (TPV) cells that efficiently converted infrared radiation at longer wavelengths than those used for traditional solar cells.
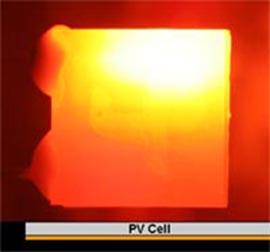 Combustion in a butane-fueled micro-reactor generates heat that a thermophotovoltaic device converts into electrical power.
This was no easy task. Standard photovoltaics that work with visible light are made of silicon. But the bandgap of silicon doesn’t match the energy levels of infrared photons. Under the DOE program, Wang’s lab developed photovoltaic cells made from the compound semiconductor gallium indium arsenic antimonide (GaInAsSb), which has the right bandgap. It’s a difficult material to work with, because with four elements involved it’s hard to produce a uniform alloy. However, Wang’s group managed to grow crystals that demonstrated near ideal performance. Wang says, though, that while gallium-antimonide-based cells are appealing, in practice indium-phosphide-based cells (also developed under the DOE program) are better candidates for practical uses. Because indium phosphide is widely used in optoelectronics applications, a manufacturing infrastructure already exists.
Simply placing the TPVs right near a large generator, however, wouldn’t work. “If you just took a solar cell and stuck it next to a burner, most of what would happen is you’d heat up the solar cell,” says Jensen. And heat causes a solar cell to break down. Wang and Jensen are now applying the TPV principle on a much smaller scale, where such thermal degradation isn’t so much of a threat. The researchers are collaborating to demonstrate an integrated micro-burner/TPV power generation device. Still, wresting the most electrical power possible from the micro-burner requires attention to the infrared spectrum that the burner emits. Wang and Jensen package the TPV with commercially available thin-film optical filters that allow short infrared wavelengths (less than 2.5 μm) to illuminate the cell while reflecting the longer-wave radiation back to the heat source. The reflected energy keeps the burner hot and helps it to use its fuel more efficiently. This technology is well suited for centimeter-scale power generation devices.
The device the researchers built is a sandwich—a square about 2 cm on a side and roughly 1 cm thick—of TPV cells and the micro-burner. The heart of the device is the burner, with two pipes leading into it to carry butane in and waste products out. On either side of the burner is a filter reflecting most of the heat and permitting the desired wavelengths (the ideal is about 2 μm) to pass through to the TPV cells. This electricity-generating cell, shielded by the filters and a thin vacuum, gets no hotter than 60°C.
The burner, designed by Brandon Blackwell, a graduate student in the Jensen laboratory, is a catalytic combustor. The inside is lined with alumina coated with platinum nanoparticles. In the lab, the burner is ignited by passing oxygen and hydrogen through it. The platinum catalyzes the reaction of the two gases, heating up the device until it reaches a temperature at which the butane will combust. A commercial device would probably heat the burner to its ignition temperature electrically, although the catalyst would still be needed to make the butane reaction efficient.
Jensen’s laboratory at MIT is still working on perfecting the design of the combustor. The biggest challenge is controlling where the heat goes. “It’s a complicated problem,” he says, and tackling it requires computer modeling of heat flow. For instance, it’s important for device efficiency that the burner heat up evenly, to make maximum use of the energy produced by combustion. He wants to add cooling fins to disperse excess heat, so that the outside of the device doesn’t get too hot to handle. At the same time, he’s trying to make the device hotter on the inside. Right now it gets to about 800°C; he’d like it to reach 900°C.
This increase has two advantages. First, as the device gets hotter, most of its radiation moves toward the shorter wavelengths that the TPV cells can convert to electricity. Moreover, the radiation output increases as the fourth power of temperature, so a hotter burner is more efficient at converting fuel to electricity. Unfortunately, the more intense heat is also more apt to destroy the packaging materials holding the various pieces of the device together. Jensen’s group is trying to redesign the package to circumvent that problem. He is also experimenting with catalysts; the more efficient the catalyst, the more fuel is burned. A commercial device would probably use a material less expensive and more stable than platinum.
How efficient does the device need to be to make it competitive with existing micropower technology? “We would consider a 5 percent overall efficiency to be a success,” Jensen says, “because at that point we would have beaten everything out there.” Butane, he explains, provides about 13,000 watt-hours per kilogram. Five percent of that would be 650 W-hr/kg —more than triple the 200 W-hr/kg that the best battery provides. At 5% efficiency, then, 300 milliliters of butane (about the amount in a typical lighter) would provide enough energy for 50 hours of talk time on a BlackBerry—ten times longer than what a high-performance lithium-ion battery supplies.
Moreover, butane should prove no burden to soldiers on the move. “It would be a lot easier for them to be carrying a can of fuel than it would be to carry the equivalent amount of power in batteries,” Wang says. And the military is used to carrying fuel.
The device would be ideal for autonomous systems because it is lighter weight and has a longer lifetime than batteries. Unmanned aerial vehicles could fly farther and carry more power with less weight. Sensor networks could run longer on their own with a supply of butane than they could on batteries, which need to be changed sooner. The micro-burner/TPV device faces competition from micro fuel cells. But Jensen says that technology is still under development as well, and is complicated by the extra step of converting hydrocarbons to the hydrogen that a fuel cell consumes to generate power.
Wang and Jensen say it’s less obvious whether their device would be useful in consumer products, mostly because it will probably always be too expensive to easily compete with batteries, except in niche applications. Moreover, says Jensen, the burner is still too hot to put in a laptop computer. But it might be useful in automotive applications as well as for other consumer uses, such as a portable battery charger. The researchers expect that they’ll be able to demonstrate their device by the end of the year. After that, they will look for a sponsor who wants them to develop the technology for specific applications in an increasingly mobile and power-hungry world. |