Load-Sensing Boots
Instrumented footwear technologies present new possibilities for tracking and preventing lower-limb musculoskeletal injuries.
We’ve all heard about a sprinter with a pulled Achilles’ tendon, a gymnast with a stress fracture, or a football player with a meniscal tear. Consider any exercise and it is clear that overtraining and routine repetition involving a particular muscle group is a recipe for disaster. Such physical exertion is only intensified during military trainings and missions when swift movements and external forces continually place stress on the load-bearing bones and joints utilized in locomotion. Strap a 40- to 100-pound pack on a soldier’s back and movements like walking, running, climbing, and even standing in place become much more taxing on the body, often resulting in the musculoskeletal injuries that are so prevalent among service members.
But if there were a way to quantify how much load, or weight, a soldier is carrying, and characterize the network of motions and forces that are involved, could such injuries be prevented? Joseph Lacirignola and Tadd Hughes, researchers in Lincoln Laboratory’s Bioengineering Systems and Technologies Group, and fellow staff members Carlos Aguilar, Kate Fischl, Whitney Young, David Maurer, and David Aubin are studying this question of load dynamics. As part of a larger injury and physiological status monitoring program funded by the U.S. Army Research Institute of Environmental Medicine (USARIEM), the team is prototyping various sensor technologies to be integrated into military boots. These technologies, collectively referred to as the “load-sensor suite,” are capable of determining how much weight an individual is carrying and where the weight is applying stress on the musculoskeletal system during both static and dynamic actions.
|
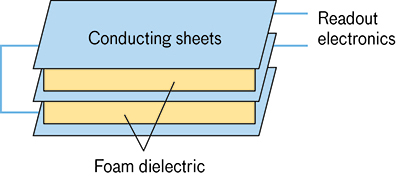 Capacitive load-sensor insole with readout electronics. |
Currently, the load-sensor suite is made up of four prototypes:
- Capacitive load sensors—three layers of conducting sheets separated by two layers of insulative foam. The force exerted by stepping on a removable insole or incorporated midsole sends an electrical signal to a capacitance meter.
- Load cells—integrated components in a midsole sensing module cushioned by a foam insert. Load-transfer plates feed the weight distribution from each foot into miniature load cells positioned at three discrete points: the heel, lateral midfoot, and ball of the foot (metatarsal) areas. Readout electronics are connected to an ankle monitor that supplies energy and stores data.
- Wave-spring strain gauges—stacked layers of wave washers (thin, disc-shaped rings) attached to a strain gauge and integrated into soles. The strain gauge senses changes in electrical resistance caused by movement and sends the signal to an ankle monitor.
- Wave-washer strain gauges—non-stacked wave washers attached to a strain gauge packaged into inserts with built-in electronics.
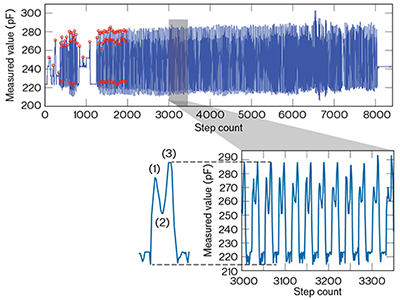 The measurement of an individual foot (signal coming from the capacitive insole) shows (1) the impact force on the heel, (2) the weight over the entire foot, and (3) the push-off force of the ball of the foot. In this case, note the relative similarities of the push-off and the variations in the heel impact throughout the entire test period.
Combined with an accelerometer and gyrometer, the load-sensor suite systems can collect swing and stance dynamics, angles of impact, and accelerations. Analysis of these measurements can provide the military with valuable insights to correct injury-inducing practices. For instance, if results indicate an unbalanced gait, a soldier’s pack may be lightened or repositioned to distribute weight more symmetrically. If the data show a particular movement is causing widespread injury among soldiers, training regimens can be adapted. Changes in the heel-to-ball force ratio may indicate increasing fatigue that can then be alleviated. As Hughes notes, “Tests over weeks and months with an average soldier carrying a 40-pound pack might give us an evaluation of how often he should be rested.” Lacirignola similarly comments that the data can help determine “pound hours,” or “how long one can last with a particular load and the resultant stress placed on the muscles.”
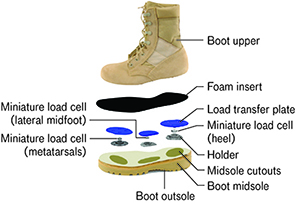 Load cells, positioned at three discrete points on the foot, are integrated into the midsole of a standard warfighter boot.
While force-sensitive treadmills (the “gold standard to measure pressure on the joints,” according to Lacirignola) and motion-capturing cameras are very accurate, they lack practicality beyond laboratory settings. “Taking measurements like running up a hill and going up stairs outside of the lab has never been done outside of a lab before,” Lacirignola continues. Without compromising natural gait rhythms, the load-sensor suite technologies can assess how environmental factors, such as uneven terrain, impact locomotive patterns and injury susceptibility.
However, the force-sensitive treadmill will be useful in evaluating the accuracy of the sensor technologies (i.e., a calibration tool). Currently, a USARIEM-Lincoln Laboratory study is comparing the results obtained from the treadmill to those from the load-cell instrumented boot. The accuracy of the wave-washer and wave-spring designs will similarly be tested after the designs are further developed and new data are collected over the next few months. The team continues to assess the effectiveness of the capacitive load sensor, too.
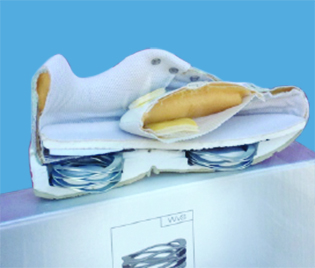 Wave-spring strain gauge.
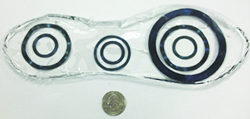 Wave-washer strain gauge insert (wave washer in inset). |
|
Besides these studies, current objectives include miniaturization and seamless integration of the electronics into the sensor systems, with an eye toward wireless data transmission. The team will also be conducting a cost-benefit analysis of price versus durability in the context of mass production (individual production costs for the prototypes range from $20 to $3500 a pair). Once the technology is fine-tuned, it could be adapted for use in sports medicine, athletic performance training, weight and exercise monitoring, and occupational safety compliance. Hughes thinks that a similar technology could also be used to “detect load on soldiers’ backs and shoulders, or even to assess helmet blast force.”
The load-sensor suite team extends their sincere gratitude to USARIEM sponsors Reed Hoyt, Stephen Mullen, Joseph Seay, and William Santee and welcomes further sponsorship as they move forward with their project.
|