Publications
Lab Notes
LASER TECHNOLOGY A Bright Idea |
Posted June 2010 |
Simple tweaks turn tiny diode lasers into powerhouses. |
Electrical engineer Kevin Creedon turns on the pump that sends cooling water flowing past the thumbnail-sized bar of laser diodes (a linear array of edge-emitting diodes, generally 1 μm high by approximately 100 μm wide), dons a pair of protective goggles, and flips a switch. Invisible to the naked eye, beams of laser light exit the diodes, pass through a lens, bounce off a grating, and move between some mirrors before emerging from a hole in a small box to produce a bright red spot on the piece of paper that Creedon's colleague, physicist Bien Chann (now at TeraDiode), is holding just outside the opening.

This setup—diodes, lens, grating, and mirrors inside a box about half the size of a shoebox—may lead to a new generation of high-powered lasers, say the researchers in Lincoln Laboratory's Laser Technology and Applications Group. It's certainly less complex than the setup on the other side of the lab bench, a couple dozen components covering the length of an optical table, which Chann says is a constant headache to try to get to work.
Chann, Creedon, and their colleagues are trying different ways to combine the beams of many tiny diode lasers into one, thus increasing the output power. The challenge, as Chann explains, is "How do you take 10 lasers or 100 lasers or however many lasers you want and put them together so you get all the power of the group of lasers but retain the beam quality of a single element?"
Diode lasers are often used to pump other types of lasers, such as neodymium-doped YAG (yttrium aluminum garnet) crystals or erbium-doped fibers. Those larger lasers are popular in industrial applications, such as cutting and welding, in which more power makes the process faster and more efficient. But because a diode-pumped laser can't put out more energy than the diodes are putting in, it is essential to increase the power output of diode lasers.
It's common to bunch diodes together—the team uses diode bars that group together a row of 19 emitters in each bar, totaling about 100 watts. But while that increases total power, the brightness—that is, the power per unit area of solid angle that the beam spreads out into—is no greater than a single diode. Applications such as coupling the beam into a fiber require a high-quality beam that combines beams from all the diodes into one tiny spot.
![]() |
![]() |
The laser diode bar, like the one shown above produced by the Electro-optical Materials and Devices Group, is an array of efficient, high-power emitters. Typical bars can emit over 100 W, but they suffer from low brightness and the "smile" (below). |
|
![]() |
To get both high power and high brightness, Chann and Creedon use a setup designed a few years ago by group leader Antonio Sanchez-Rubio and associate leader Tso Yee Fan. They buy standard diode bars that have an internal cavity coating at the back that reflects 99 percent of the light, while the front coating reflects 5 percent back. The emitted light passes through a lens onto a grating and bounces from there to a mirror that has a 10 percent reflective coating. The light then follows the same path backwards, onto the grating, through the lens, and back to the diode, where it injection locks the emitters so that they lase at the wavelength they should to combine into a single beam. Essentially, they've turned the whole setup into a single laser resonator cavity.
Commercially available diodes generally have a gain of about 50 or 60 nanometers. That means the light coming out of a diode that nominally emits at 1000 nm can be "locked" at any wavelength between 970 and 1030 nm. The 5 percent reflectivity coating that is optimized for high power output reduces this range to approximately 4 nm.
But when the beam strikes the grating at a particular angle, only light at a very specific wavelength is directed along the path that will return it to the laser, so the diode will only lase at that specific wavelength. The beam from the diode next to that one will hit at a different angle on the grating, requiring a different path, and thus will lase only at a slightly different wavelength. "It's automatic. You don't have to do anything to it," Chann says. Once all the elements lase at the right wavelength, the grating acts like a prism in reverse, combining them into a single beam, with the power of each, but with vastly improved brightness.
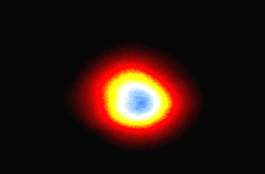
But there is still a problem. Even diode bars manufactured to the strictest tolerance suffer from a phenomenon called "smile." The separate emitters don't align perfectly horizontally, but tend to sag into a crooked smile of laser spots because of the dissimilar thermal expansion during soldering to the heat sink. Even in the very best laser bars, emitters can be out of place by 2 to 3 micrometers. Because the setup relies on each beam hitting at its particular angle on the grating, the fact that they're out of alignment throws a monkey wrench into the system.
Chann fixed the problem with a very simple idea. He flipped the diode bars on their sides, so the rows of emitters are vertical rather than horizontal. Because of the shape of the lens's focal plane and the design of the grating, a vertical displacement of the emitters doesn't have the same effect as the horizontal displacement, and the setup works to make a bright, powerful beam with a spectrum that fits within the 4 nm locking range, so it's compatible with standard, high-power facet coatings.
"It's so simple it makes you wonder, 'Why didn't I think of that?'" says Sanchez-Rubio.
Having designed the system, the staff focused on building an actual working version. In a two-year program that began in March 2009, Sanchez-Rubio and Steven Augst are building a system that combines lasers together to produce a coupled 100 mm fiber system with an output of 2 kW and a bandwidth of 2 nm. By contrast, the best such beam commercially available is 50 watts. Much of the work necessary to realize this 40-fold increase will involve finding components able to handle such high powers. The researchers will also have to work on reforming the beam into the optimum shape to be coupled into a fiber.
The Laboratory team is also using the same setup to build a 200 W system for the Laser and Optics Research Center at the U.S. Air Force Academy. This system will act as a diode pump for an alkali-vapor laser, resulting in a tool powerful enough for industrial applications. Lasers that are based on alkali metals, such as potassium, rubidium, and cesium suspended in buffer gases, should produce beams of high power and high optical quality and not suffer from the heat-management issues that afflict other lasers, but they have been limited by a lack of suitably narrow, high-brightness pump diodes. Narrower linewidths from the pump lasers would allow the alkali lasers to operate at lower temperatures and gas pressures, slowing down chemical reactions between the alkalis and the buffer gases and making the laser more efficient.
Boris Zhdanov, a research scientist at the Academy, is waiting for the Laboratory to complete the work so Zhdanov and his colleagues can test the setup on their alkali laser where, he says, a narrow-line pump source is key. "What they are doing is very important for us, and not only for us, but others who work in this field," Zhdanov says.
However it is applied, the beam-combining setup, Chann says, should make diode arrays into lasers much more powerful than they are now. "There's no reason we couldn't do 10 kilowatts."