News
Six innovative technologies developed by MIT Lincoln Laboratory are honored with 2014 R&D 100 Awards
Awards recognize innovations in antenna design, high-speed microswitching, space-object imaging, ground-penetrating radar, laser communications, and chemical sensing
Six technologies developed by MIT Lincoln Laboratory were named recipients of 2014 R&D 100 Awards, given annually by R&D Magazine to recognize the 100 most technologically significant innovations introduced during the prior year.
Each year, R&D Magazine—an international publication for research scientists, engineers, and technical staff—chooses the winners from among hundreds of nominations submitted by industries, government laboratories, and university research centers from across the globe.
- Airborne Sense-and-Avoid Radar Panel—a novel stepped-notch antenna array that supports aircraft and weather detection and tracking modes in a single multifunction aperture
- Curled Microelectromechanical Switch—a curled-electrode switch that eliminates the sticking and contamination issues inherent in traditional electromechanical switches
- Haystack Ultrawideband Satellite Imaging Radar—a ground-based, dual X- and W-band sensor that can produce very-high-resolution images of objects orbiting Earth
- Localizing Ground-Penetrating Radar—a robust sensor that provides highly accurate, real-time vehicular position estimates based on prior mapping of subsurface features
- Lunar Laser Communication System—an optical system that achieves very high uplink and downlink data rates between an Earth terminal and a distant satellite
- Wide-Area Chemical Sensor—a highly precise, self-referencing spectrometer that measures the concentrations of specified target gases within the atmosphere
Reducing the cost and complexity of wide-bandwidth radar systems
The Airborne Sense-and-Avoid (ABSAA) Radar Panel is a stepped-notch antenna array that may transform the way in which high-performance, wide-bandwidth radar systems are fabricated. The small physical size of the panel and its operational frequency range (Ku band, 13–15 GHz) make the ABSAA panel suitable for narrow beamwidth radar systems integrated on small platforms. Three innovations enable high performance for a fraction of the cost of traditional antennas: the incorporation of thermal cooling into the panel; the use of multifunction radio-frequency integrated circuits, manufactured in a commercially available, high-volume silicon germanium 0.13 µm foundry process; and the elimination of a separate transmit and receive module.
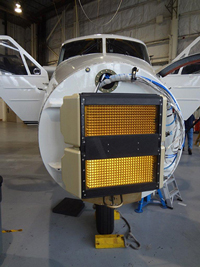
The ABSAA panel was designed especially for sense-and-avoid (SAA) systems mandated by the Federal Aviation Administration for operation of unmanned aerial systems (UAS) within the national airspace. ABSAA enables a sense-and-avoid system to detect aircraft in a substantial field of regard, at a sufficient range, and with sufficient accuracy to allow unmanned aircraft to quickly maneuver to maintain separation from another aircraft.
The panel supports both aircraft and weather detection and tracking modes in a single multifunction aperture. Its design has the potential to facilitate the expanded usage of unmanned aircraft systems into a broad range of applications, including security and disaster response efforts, aerial mapping projects, and land and crop surveys.
The ABSAA Radar Panel was developed by a multidivisional team led by Sean Duffy.
Team members include Patrick Bell, David Bragdon, Glenn Brigham, Rodney Cole, Matthew Edwards, Thomas Ferguson, H. David Goldfein, Jeffrey Herd, Edward Martin, Kevin Newman, Michael Owen, Daniel Santiago, and Sean Tobin.
The Curled Microelectromechanical Switch (CMEMS) virtually eliminates the sticking, dielectric charging, and contamination issues associated with traditional MEMS switches, which are used in wireless personal communication devices, satellite communication, and phased array antennas. MEMS are ideal for these applications because of their low–size, weight, and power (SWaP) requirements, high isolation, large frequency range, and linearity; however, reliability has been a problem with the charged dielectric, leading to stiction and deformation failure. In addition, contact welding and contamination of the switch have been problematic.
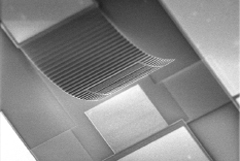
CMEMS has a curled, corrugated cantilever design that moves the curved electrode in and out of contact, providing the largest impedance change, on to off, of any switch, MEMS capacitive or otherwise, in the 1–100 GHz frequency range. This design feature translates into a number of advantages including temperature stability and low power loss, critical variables for cell phones that rely on batteries. Low power loss also has an advantage for arrays of switches required in a power train having several switches in a series, such as phased array antenna elements. Reliability has been tested on packaged switches through 100 billion cycles—by far the highest cycle number for any MEMS capacitive-type switch. In the future, this technology could support satellite communication via antennas on car roofs and radars around cars and homes.
The principal developers of CMEMS are Carl Bozler, Jeremy Muldavin, Craig Keast, and Steven Rabe.
Improving space situational awareness
The dual-band (X and W) Haystack Ultrawideband Satellite Imaging Radar (HUSIR) is the highest-resolution, long-range space-object characterization radar in the world. The latest iteration in the technological evolution of high-performance microwave systems, HUSIR is an upgrade to the X-band Haystack Long-Range Imaging Radar (LRIR). HUSIR maintains the LRIR's X-band capability and adds a millimeter-wave radar operating in W band that provides much higher resolution but at lower power and sensitivity. Operating in both bands simultaneously, HUSIR achieves greatly improved image resolution on near-Earth satellites while preserving the deep-space imaging capability of the LRIR.
HUSIR is a major engineering development that required advancements in the design and fabrication of a large, highly precise antenna, high-power millimeter-wave electronics, and signal processing hardware and algorithms. A number of innovative technologies enable HUSIR's advanced imaging capabilities: a W-band gyrotron traveling-wave tube (gyroTWT); a high-bandwidth waveform generator; and advanced signal processing based on Lincoln Laboratory's Radar Open Systems Architecture.
As a contributing sensor to the U.S. Space Surveillance Network, HUSIR will supply data that will help provide the comprehensive space situational awareness necessary to aid in the protection of space assets and the preservation of the space environment. Because HUSIR generates both X- and W-band images for every object tracked, analysts can better determine an object's size, shape, orientation, and motion. HUSIR is also capable of characterizing the individual components of large, complex objects and identifying small objects previously indistinguishable from each other.
HUSIR was co-developed by Lincoln Laboratory, Simpson Gumpertz & Heger (SGH), and Communications & Power Industries (CPI). More than 100 individuals contributed to the HUSIR effort. Key contributors to the HUSIR program include Lincoln Laboratory staff members Joseph Usoff, Mark Czerwinski, James Eshbaugh, Michael MacDonald, Timothy Hiett, Michael Glynn, Nikolas Waggener, Robert Morrison, Weber Hoen, Todd Mower, Michael Languirand, Gerard Languirand, David Crompton, George Haldeman, Michael Clarke, Mark Silver, and Raid Habayeb.
Utilizing underground features to estimate vehicle location
The Localizing Ground-Penetrating Radar (LGPR) provides real-time vehicle localization to better than 10 cm. LGPR offers a localization capability that is reliable in snow, smoke, dust, or heavy rain—conditions in which traditional optical systems for localization are not reliable because visible features are obscured. Using a new class of ground-penetrating radar technology, LGPR maps subsurface road features, collecting three-dimensional data of subterranean "objects" and tagging these data with global-positioning-system (GPS) locations. Because subsurface features are inherently stable over time, the data can subsequently be used to estimate the location of a moving vehicle that is driving within a previously mapped area.
Several technologies for high-precision localization exist, but most are unable to sense vehicle position in adverse conditions, i.e., on unpaved roads, in GPS-denied areas, and on road surfaces impacted by heavy rain, fog, snow, or dirt. By looking at below-ground features, LGPR can successfully operate in such conditions—a capability required by autonomous ground vehicles (AGV).
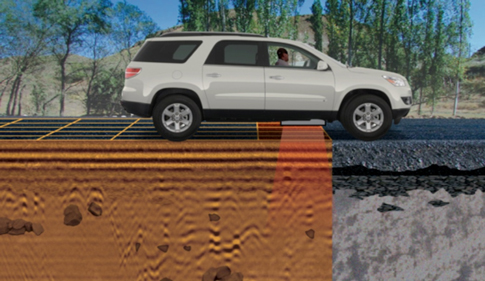
LGPR has applications in vehicle localization for self-driving cars, military vehicles, and heavy vehicles used by industries such as mining and construction. Because LGPR compares the subsurface data it collects to a previously produced map, LGPR can also be used for infrastructure checks such as finding below-road sinkholes and detecting bridge damage. In the future, LGPR may be used in conjunction with complementary sensors, including GPS, lidar, odometry, and cameras, to improve the localization capabilities for AGVs.
"We're excited about the potential impact of LGPR on self-driving vehicles, as the system is not only a way to make current approaches more robust but also a way to open up the possibility of all-weather autonomous operation," says Byron Stanley, one of three principal investigators for the LGPR program. Stanley, along with principal investigators Matthew Cornick and Jeffrey Koechling, and team members Charles Coldwell and Beijia Zhang, have applied for a patent on the LGPR technology.
Achieving world-record data transmission speeds over great distances by using a two-way laser communication link between the Earth and the MoonOn 17 October 2013, the Lunar Laser Communication System (LLCS) used a pulsed laser beam to send data from a space terminal aboard the National Aeronautics and Space Administration's (NASA) Lunar Atmosphere and Dust Environment Explorer (LADEE) spacecraft to a ground terminal on Earth at a download speed of 622 megabits per second (Mbps). LLCS also demonstrated a data upload speed of 20 Mbps. These download and upload speeds are respectively six and 5000 times faster than the speeds achieved by the best radio systems ever flown to the Moon. The demonstration, which delivered error-free performance, was accomplished with a space terminal that has half the weight and uses 25% less power than the most capable lunar radio systems. A new type of high-speed, high-efficiency detector—the superconducting nanowire single-photon detector—enabled the use of much smaller receive telescopes in the ground terminal in comparison to other receivers and communication through the turbulent atmosphere. Arrays of these detectors were used to time-tag each separate photon in the downlink beam with unprecedented accuracy and efficiency.
![]() |
![]() |
The Lunar Laser Communication System space terminal (left) is seen during integration on the Lunar Atmosphere and Dust Environment Explorer (LADEE) spacecraft. LLCS used a 0.5 W optical beam from a 10 cm diameter optical telescope on the lunar-orbiting space terminal to transmit data over the 239,000 miles from the Moon to a ground terminal (right) deployed at White Sands, New Mexico. Each of the four 0.4 m diameter receive telescopes in the ground terminal was fiber-coupled to a separate superconducting nanowire single-photon detector array. |
NASA is using LLCS designs as the basis for the design of its upcoming Laser Communications Relay Demonstration, which will demonstrate a laser communications relay capability on a geosynchronous satellite. With the addition of a slightly higher-power fiber-coupled transmitter and a larger ground telescope, LLCS could support its current data rates from distances further away than the Moon. In the future, the ability of LLCS to rapidly transmit enormous amounts of information will transform the objectives, design, and operation of scientific space missions.
"This award is a testament of the dedication and excellence of our talented team of more than 100 Lincoln Laboratory experts," says Don Boroson, who, along with Bryan Robinson, Dennis Burianek, Daniel Murphy, Farzana Khatri, and Paul Sasson, led the LLCS program to build the space and ground terminals for NASA's Lunar Laser Communication Demonstration mission. The team would like to acknowledge Donald Cornwell of NASA's Goddard Space Flight Center and John Rush of NASA's Space Communications and Navigation Program Office for their efforts in this mission.
Detecting target gases released at low concentrations and over wide areas
The Wide-Area Chemical Sensor (WACS) measures concentrations of specified target gases in the atmosphere using a single, relatively broadband (~5 GHz) laser source. Deformations of the laser spectral beam are matched to targeted materials, enabling the detection and discrimination of gas clouds at very low concentrations (~1 part per trillion by volume) over tens of kilometers, while correcting for false alarms caused by atmospheric turbulence, variable atmospheric transmission, and other non-target gases. WACS uses a self-referencing spectroscopy technique to decouple the target gas from the background atmosphere. Unlike traditional long-range chemical sensing techniques that separate the "sensitive to x gas" and "insensitive to x gas" atmospheric measurements in time, switching back and forth between them quickly to reduce errors induced by the changing atmosphere, WACS measures these atmospheric components concurrently for enhanced accuracy. This method is particularly suited to gases with primarily small molecules—methane, various nitrogen oxides, carbon monoxide, and hydrogen halides.
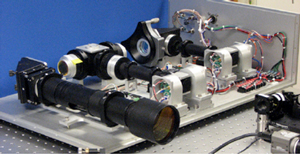
WACS can rapidly collect target concentrations of gases in fractions of a second. Placed on a mobile platform, WACS can achieve area coverage rates of 100–1000 km2/hour. Because it is highly sensitive to target gases even in the presence of contaminants, WACS can detect and localize natural gas pipeline leaks of as low as 100 g/hour. Other applications include detecting chemicals released during industrial accidents and identifying emissions violations. In addition to long-range monitoring of outdoor environments, short-range measurements within open indoor spaces, such as machine shops or industrial plants, are well served by the WACS technology.
The core WACS team consists of Jonathan Ashcom, Alan DeCew, Sumanth Kaushik, Eric Statz, Samuel Wong, and John Zayhowski.
Lincoln Laboratory's past R&D 100 Award recipients
Since 2010, Lincoln Laboratory has received 22 R&D 100 Awards (including the six 2014 winners and the 2011 R&D 100 Editor's Choice Award for the Multifunction Phased Array Radar Panel*):
2013
Photoacoustic Sensing of Explosives
Structured Knowledge Space
2012
Lincoln Open Cryptographic Key Management Architecture
Route Availability Planning Tool
Wavelength Beam-Combining Fiber-Coupled Diode Laser
Wide Field-of-View Curved Focal Plane Array
2011
Airborne Ladar Imaging Research Testbed
Multifunction Phased Array Radar Panel*
Parallel Vector Tile Optimizing Library
Pathogen Analyzer for Threatening Environmental Releases
2010
Digital-Pixel Focal Plane Array
Geiger-Mode Avalanche Photodiode Detector Focal Plane Arrays
Miniaturized Radio-Frequency Four-Channel Receiver
Runway Status Lights
Subwavelength-Separated Superconducting Nanowire Single-Photon Detector Arrays
In addition, Lincoln Laboratory received two earlier R&D 100 Awards: one in 1998 jointly with Cyra Technologies and the Los Alamos National Laboratory for Cyrax, a portable three-dimensional laser mapping and imaging system; the other in 1995 for the Global Positioning System (GPS)-Squitter, a technology that determines a plane's position using GPS and then squitters, or broadcasts, that information to air traffic controllers and other aircraft.
Winners are selected by R&D Magazine editors, who receive guidance from an independent panel of experts. Awards are typically given across 20 or so technology categories. During the 52 years of the award's presentation, winners have included sophisticated testing equipment, innovative new materials, biomedical products, and consumer items. Such familiar inventions as the NicoDerm anti-smoking patch and the high-definition television (HDTV) were past R&D 100 Award recipients.
The 52nd Annual R&D 100 Banquet and Awards Presentation will honor the 2014 winners on 7 November 2014 at the Bellagio Hotel in Las Vegas, Nevada. The day-long event will include an exhibition of winning technologies, a formal cocktail reception, and a black-tie banquet and awards presentation.
Posted July 2014
top of page